What
equipment is used for etching?
Abrasive etching
equipment is still called sandblasting equipment, in spite of the
fact that sand is rarely used to etch glass anymore. However it
is not just any sandblasting equipment. Blasting equipment used
to etch glass has evolved for its specialized purpose in the past
twenty years. Compared to regular blasting equipment, the equipment
designed for glass has smaller, more easily manipulated hoses and
nozzles, special foot pedal controls, specialized lighting in the
cabinet, and other improvements.
When you are
purchasing equipment for etching glass you are much better off to
purchase it from one of the few companies who specialize in equipment
for glass. It won’t cost you much more, if any more, than equivalent
equipment used for other purposes, but it will save you hours of
time converting the other equipment for glass, not to mention the
cost in dollars to do it. Lets take a closer look.
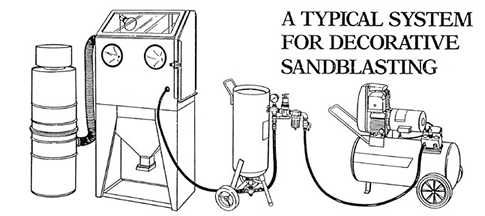
There are three major components to a glass etching setup: 1) an
air compressor (at right), 2) a sandblaster (in the middle), and
3) a blasting cabinet with dust collector (at the left). The air
compressor produces the pressurized air that powers the sandblaster
and must do so in adequate quantity for the blaster you will be
using. The blaster stores the abrasive and provides a method of
combining the abrasive with the compressed air and directing it
effectively at the glass. The blasting cabinet provides a contained
environment in which to blast, so that the spent abrasive and blasting
dust are controlled, while allowing full vision of the project being
etched.
Air
Compressors
A complete discussion of air compressors could take a whole book,
but a short introduction will have to suffice here. Compressors
are rated in terms of how much air they put out at a given pressure.
This is usually expressed something like: Output - 11 CFM (cubic
feet of air per minute) @ 90 PSI (pounds per square inch
of air pressure). These numbers are always used together, because
when one changes, the other changes as well.
You should never
buy a compressor by the horsepower because there are small consumer
compressors and large industrial compressors that have the same
horsepower rating, but which put out vastly different amounts of
air. Always buy a compressor based on how much air it puts out.
When you purchase equipment, you should get a compressor that puts
out at least 2-3 times the volume of air required by the blaster
you will be using, at the desired blasting pressure. So, you have
to know which blaster you will be using, before you buy a compressor.
Blasters

There are only two types of blasters, siphon blasters and pressure
blasters. Siphon blasters are cheaper, but inefficient and use a
lot of air. Pressure blasters are more expensive, but are much faster
and easier to use. Pressure blasters also use less air from the
compressor, which allows you to use a smaller compressor or causes
less wear and tear on an existing compressor. A standard sized pressure
blaster is not prohibitively expensive for most people, but should
be especially set up for use on glass. This means you should purchase
from a distributor who specifically configures their equipment for
glass etching. Read the specs for the blaster (nozzle size and air
requirements) to find out how much air you need from the compressor.
Blasting
Cabinets
Blasting cabinets come in all sizes and configurations. The ones
best for glass are wider and taller (with respect to their depth
from front to back), than ordinary cabinets. This accomodates flat
sheets of glass best, without requiring that the person doing the
blasting have extra long arms.
Most cabinets
allow blasting of only as large a piece of glass as will fit through
the door, so the door has to be as large as possible. However some
cabinets are especially made for larger pieces of glass and have
slotted openings in the sides and top of the cabinet, allowing large
pieces to be passed through, blasting a little at a time. Gaskets
on the moveable slots keep abrasive from getting out. These cabinets
are really your best investment because they can accomodate both
large and small pieces of glass equally well. They are the most
expensive cabinets, though.
Blasting cabinets
for glass should have incandescent, point source lighting rather
than fluorescent lights. A dust collector is essential, to keep
the dust level low enough in the cabinet so you can see what you
are blasting. Again, there are many manufacturers out there, but
only a few that set their equipment up especially for decorative
blasting on substrates such as glass.
Blast
rooms
Of course, you can build a whole blast room to blast large pieces
of glass. But that means you have have space for it in your shop
(most blast rooms are at least 8' long x 8' high x 6' deep). You
also have to equip it with a large dust collection system and a
source of clean breathing air, because you will be going inside
the room to blast. You always have to wear protective gear for your
face and exposed skin.
Equipment is
a big subject to tackle, and it is explained much more in depth
in our books and videos.
|